ViscoSensor




Product detailed description
THE VISCOSENSOR RSU
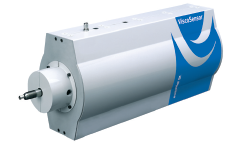
VISCOSENSOR RCU: ULTIMATE PERFORMANCE
Our high performance RCU unit combines rheological properties of laboratory capillary rheometer with MFI data provided by laboratory plas. It has been complemented by a Siemens S7-1500 PLC with a 7" (178 mm) Siemens touch panel with HMI touch interface. This combination provides higher computing power and superior graphics, allowing the RCU to provide accuracy of +/- 0.5% over the entire range.  ; This allows the RCU to better match measurements with those made by laboratory instruments. In addition, it is certified for potentially explosive atmospheres as required.
< p>
VISCOSENSOR e-RCU: PERFORMANCE SIMPLIFIED
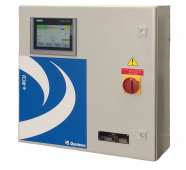
The ViscoSensor e-RCU offers a simplified PLC with digital and analog inputs/outputs that most operations need for a cost-effective approach to on-line measurement. It is equipped with a Siemens S7-1200 PLC with a Siemens HMI touch panel with 7" (178 mm) diagonal. This combination provides the system with computing power and top-notch graphics, allowing the e-RCU to provide +/- 2% accuracy across the range. The e-RCU provides the processor with the ability to measure melt flow ratio, relative viscosity, intrinsic viscosity, and melt viscosity in typical end-user environments. All this creates a cost-effective system that reduces the risk of inaccuracy to an acceptable level. If conditions change and the system needs to be used in a hazardous and/or classified location, compatibility with standard RCUs allows for an easy upgrade.
PERFORMANCE CHARACTERISTICS
Melt flow index | 0.1 - 25000 g/10 min | < /tr>
---|---|
Viscosity range | 10 – 105 span>Pas |
Shear stress | 150 - 1.5 x 105< /sup> Pa |
Shear velocity | 0.1 – 7500 s-1 (standard die) max 50,000 s-1 (special die) |
Capillaries | |
Temperature Range | 40 – 350° C |
Pressure Range | 3 x 105 – 3.5 x 107 Pa |
Dosing pump | 0.16 cm3 / RPM (standard ) 0.297 cm3/ RPM (optional) 0.584 cm3/ RPM (optional) < /td> |
Pump Speed | 3 - 75 RPM |
Polymer Flow | 225 g/hr (average) |
MEASUREMENT AND REGULATION FUNCTIONS
Test Modes | |
---|---|
Shear Stress Mode | |
Set Point th> | Pressure |
Measurements | Melt Flow Index | < /tr>
Shear Rate Mode | |
Setpoint | Pump Speed |
Measurement< /th> | Apparent viscosity |
Temperature control | 3 heating zones td> |
ANALOG OUTPUTS: (STANDARD 4 - 20 MA)
Options | < p>• Melt Flow Index • Apparent viscosity • Melting point • Melt pressure • Pump speed • Temperature Pump Zone • temp. Die Zone | Choose 2 of the following: |
---|
ELECTRICAL SPECIFICATION h2>
System Voltage | 220-240 V, single-phase, 50/60 Hz |
---|---|
Power supply | 2000 W (max) |
DIGITAL INPUTS
Weight | 45 lbs. |
---|---|
Height | 25 in. (63.6 cm) |
Width | 11.1 in. (28.2 cm) |
Depth | 9.9 in. (25.2 cm) |
Mounting configuration | Vertical (Stand for horizontal - only when using pressure port M18) |
Providing Innovative Solutions
For more than 60 years, with a commitment to helping customers, Dynisco has been providing tools and services for the polymer industry that offer its customers a 'window into the process' - an insight into the manufacturing process.
Today's customers need accurate information that allows them to verify and, if necessary, adjust their process to ensure that their products meet precise specifications. The information provided by Dynisco enables our customers to maintain a consistent process regardless of their global location.
Dynisco's portfolio represents a vast array of sensors (transducers), evaluation and display technology along with laboratory instruments with the possibility of online connection directly in production, thus providing you with the most accurate information about your production process in the market, in the field of measuring rheological properties of polymers, pressure, and temperature.
Dynisco provides our customers with the ability to compare data obtained from a pilot project with a laboratory environment with online production 24 hours a day. This data allows for immediate response and system adjustment in critical situations, ensuring that any deviations are immediately corrected to guarantee maximum quality at maximum performance.
History of Dynisco
Dynisco, known worldwide for top-notch products in pressure and temperature measurement and regulation for the plastic extrusion industry, has been developing innovative and high-quality solutions for plastic extrusion processing for 60 years and is founded on the expertise of engineers with an average of 15-20 years of experience. Dynisco's sensors, controls, and analytical instruments have proven to offer better control, reduce downtime, minimal scrap, and unmatched reliability and working life. Our commitment and ability to collaborate with you to help you measure, analyze, and equip extrusion control systems that meet your precise needs are unparalleled. From breakthrough technology in the most comprehensive range of sensors to renowned quality and performance in indicators, controls, and analytical tools.
Dynisco Sensors Dynisco was designed specifically for the robust environment of the plastics industry and has developed some of the most advanced solutions for measuring plastic extrusion, molding, and control applications. We produce a wide range of robust melt pressure sensors compatible with mV/V, mA, VDC, and HART thanks to engineering excellence based on expertise and experience.
Dynisco Analytical Instruments The quality of the process begins with the use of material. Dynisco's analytical tools enable the processor to verify material specification and optimize process conditions. These tools include flow Dynisco Heilbronn Facility in Germany
melt indexers, capillary rheometers, and small laboratory mixing extrusion systems. Dynisco also offers the most comprehensive and accurate range of on-line rheometers available on the market.
Dynisco offers a complete range of global services and technical support for our complete line. Dozens of highly qualified technical support workers are deployed internationally and provide:
Expert consultations Custom solution design On-site equipment diagnostics and troubleshooting Repairs and maintenance of transducers ∙ Installation services Equipment operation training ∙ System repairs, spare parts, preventive maintenance, and more
Customers from around the world have discovered that Dynisco is dedicated to product innovation and advanced system solutions that significantly impact the efficiency of manufacturing processes.